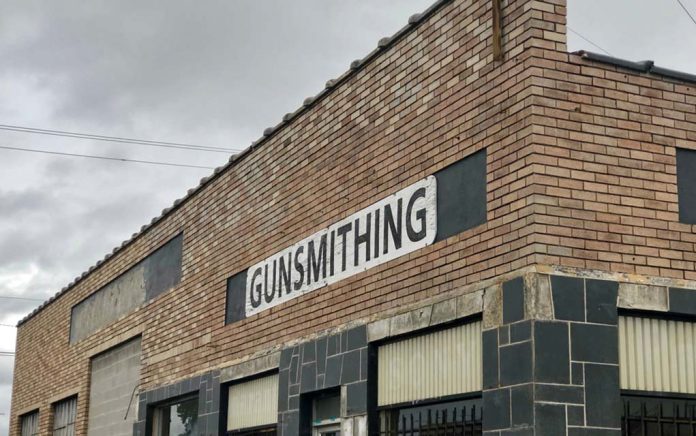
(TacticalNews.com) – A variety of different objects use springs to make them function. Especially when it comes to firearms. As many of us already know, a broken spring can render a gun inoperable. Thankfully you can make springs for your guns, making home repair a reality. While forging springs themselves may be difficult, you can create flat springs with relative ease.
How to Make Flat Springs
The first step in making flat springs is finding the material you’re going to use. Typically metal strapping works best for DIY flat springs. The metal strapping itself does offer some resistance, much like a spring does already. However, it’s not as strong as a spring. So, you will need to temper it. To do this, you simply get the metal red-hot using a heat source and let it air cool.
Next, you need to layout the shape of the spring you’re trying to recreate or replace. Using a scribe, you can trace the shape directly onto the steel strapping. Roughly cut the form you need out of the strapping. That means cutting it close to the edges of your traced image but not going over your line.
Then, you can use a bench grinder and file the strapping edges to finish forming the shape. This process helps you avoid having sharp or jagged edges on your spring, giving you a clean finish. After you’ve got your form, you need to drill any holes that may be required. You will also need to make sure to bend the strapping to the correct position.
Now that you’ve got your spring in the correct form, it’s time to harden the spring. Hardening steel is a simple process. You heat the material until it’s red-hot and place it into oil or water to cool. However, be careful about overdoing it. Hardening steel too much can result in a faulty spring as they need some flexibility to function. If you find your flat spring is too stiff, you can always temper it to reduce stiffness.
Tempering Steel
Tempering steel is also a relatively easy task to perform. However, be careful because you’ll have to start over at the hardening phase should you perform this task incorrectly.
The ideal temperature to temper steel is about 600ºF. For this reason, many people use lead, which has a melting point of 621.5ºF and place the steel into a lead bath.
It won’t take long for a small spring to reach the 600ºF mark, typically about 10-20 seconds. Your spring should be a blueish color when taken out of the molten lead. If you take your spring out and it’s gray instead of blue, you’ll need to start over at the hardening phase. Be sure to check on your part every few seconds to see if it’s the correct color. Doing this helps you avoid having to start over again.
The Last Step
Once you’ve successfully shaped, hardened, and tempered your spring, it’s time for the last step — testing it. This step is crucial because if you don’t try it before using it, it could break, and you’re right back where you started. Testing is essential as it’s always better to have something break while testing it than to have it break during operation.
Final Word
The ability to create your own flat springs could come in handy one day, particularly if you need to replace one, and there is no one else around to do it. Self-reliability is an essential part of survival, especially in the event SHTF and society collapses.
In addition to performing firearm repair, the ability to provide yourself with food is an essential component of self-reliance. Check out these six weeds you can eat to survive.
Copyright 2020, TacticalNews.com